Đầu tháng 8/2016, Hải quân Mỹ đã thử nghiệm thành công động cơ nghiêng MV-22 Osprey. Bản thân chiếc máy bay này không có gì lạ. Phương tiện hai cánh quạt đã phục vụ Hải quân Mỹ trong một thời gian dài (nó được đưa vào trang bị vào nửa cuối những năm 1980), nhưng lần đầu tiên trong lịch sử, các bộ phận quan trọng được lắp đặt trên một động cơ nghiêng (an toàn bay trực tiếp phụ thuộc vào chúng), đó là máy in 3D.
Để thử nghiệm, quân đội Hoa Kỳ đã in một khung để gắn động cơ vào cánh của thiết bị nghiêng từ titan bằng phương pháp thiêu kết laser từng lớp trực tiếp. Đồng thời, một máy đo biến dạng đã được gắn trên chính giá đỡ, được thiết kế để ghi lại biến dạng có thể xảy ra của bộ phận. Mỗi động cơ trong số hai động cơ của động cơ nghiêng MV-22 Osprey được gắn vào cánh bằng bốn giá đỡ như vậy. Đồng thời, tại thời điểm chuyến bay thử nghiệm đầu tiên của động cơ nghiêng diễn ra vào ngày 1 tháng 8 năm 2016, chỉ có một giá đỡ, được in bằng máy in 3D, được lắp đặt trên đó. Trước đó, có thông tin cho rằng các ngàm nacelle được in bằng phương pháp in ba chiều cũng đã được lắp trên bộ nghiêng.
Việc phát triển các bộ phận được in cho động cơ nghiêng được thực hiện bởi Trung tâm Điều hành Tác chiến Hàng không của Hải quân Hoa Kỳ đặt tại Căn cứ Liên hợp McGuire-Dix-Lakehurst ở New Jersey. Các chuyến bay thử nghiệm MV-22 Osprey với các bộ phận in được thực hiện tại căn cứ Patxent River của Hải quân Hoa Kỳ, các cuộc thử nghiệm được quân đội công nhận là hoàn toàn thành công. Quân đội Mỹ tin rằng nhờ sự ra đời rộng rãi của in ba chiều, công nghệ trong tương lai sẽ có thể sản xuất nhanh chóng và tương đối rẻ các bộ phận thay thế cho bộ chuyển đổi. Trong trường hợp này, các chi tiết cần thiết có thể được in trực tiếp trên các con tàu. Ngoài ra, các bộ phận được in sau đó có thể được sửa đổi để cải thiện hiệu suất của các cụm và hệ thống trên bo mạch.
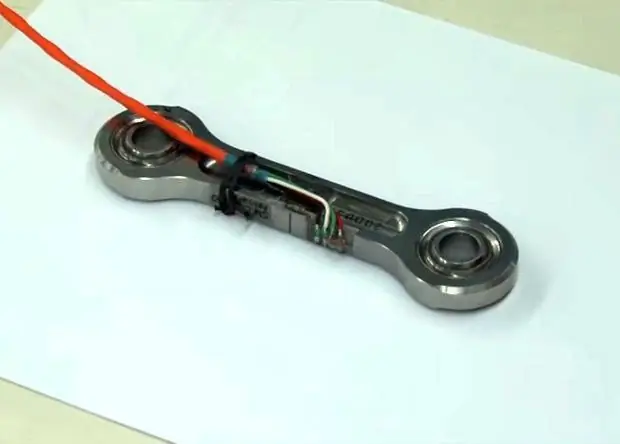
Giá đỡ động cơ in bằng titan
Quân đội Mỹ đã quan tâm đến công nghệ in 3D từ vài năm trước, nhưng cho đến gần đây, chức năng của máy in 3D vẫn chưa đủ rộng để được sử dụng thường xuyên để chế tạo các bộ phận khá phức tạp. Các bộ phận của bộ nghiêng được tạo ra bằng máy in 3D phụ gia. Phần được làm dần dần theo từng lớp. Cứ ba lớp bụi titan được kết dính bằng tia laser, quá trình này được lặp lại miễn là cần thiết để có được hình dạng mong muốn. Sau khi hoàn thành, phần thừa được cắt ra khỏi bộ phận; phần tử kết quả đã hoàn toàn sẵn sàng để sử dụng. Vì các cuộc thử nghiệm đã hoàn thành thành công nên quân đội Mỹ sẽ không dừng lại ở đó, họ sẽ chế tạo thêm 6 thành phần cấu trúc quan trọng của động cơ nghiêng, một nửa trong số đó sẽ là titan, và phần còn lại - thép.
In 3D ở Nga và trên toàn thế giới
Mặc dù việc sản xuất loại máy in này đã được thực hiện thành công ở Mỹ và Nga vài năm trước, việc tạo ra các bộ phận cho thiết bị quân sự đang trong quá trình hoàn thiện và thử nghiệm. Trước hết, điều này là do yêu cầu rất cao đối với tất cả các sản phẩm quân sự, chủ yếu là về độ tin cậy và độ bền. Tuy nhiên, người Mỹ không đơn độc đạt được tiến bộ trong lĩnh vực này. Năm thứ hai liên tiếp, các nhà thiết kế Nga đã sản xuất các bộ phận cho súng trường tấn công và súng lục được phát triển bằng công nghệ in 3D. Công nghệ mới tiết kiệm thời gian vẽ quý giá. Và việc đưa các bộ phận như vậy lên dòng có thể cung cấp sự thay thế nhanh chóng tại hiện trường, trong các tiểu đoàn sửa chữa, vì sẽ không cần đợi phụ tùng thay thế từ nhà máy cho các xe tăng hoặc máy bay không người lái tương tự.
Đối với tàu ngầm, máy in 3D quân sự sẽ đơn giản có giá trị bằng vàng, vì trong trường hợp tự động điều hướng đường dài, việc thay thế các bộ phận của chính tàu ngầm sẽ cung cấp cho tàu ngầm một nguồn tài nguyên gần như vô tận. Tình trạng tương tự cũng được quan sát với các tàu đi hải trình dài ngày và tàu phá băng. Hầu hết các tàu này sẽ nhận được máy bay không người lái trong tương lai rất gần, những tàu này cuối cùng sẽ phải sửa chữa hoặc thay thế hoàn toàn. Nếu một máy in 3D xuất hiện trên tàu, điều này sẽ giúp bạn có thể in nhanh các phụ tùng thay thế, sau đó thiết bị này có thể được sử dụng trở lại. Trong điều kiện hoạt động tạm thời và khả năng cơ động cao của hệ thống hoạt động quân sự, việc lắp ráp cục bộ các bộ phận, cụm và cơ cấu nhất định ngay tại chỗ sẽ cho phép duy trì mức độ hiệu quả cao của các đơn vị hỗ trợ.
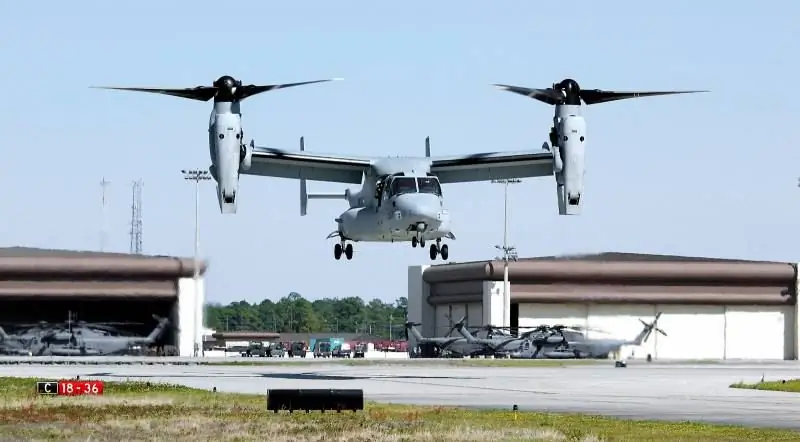
Osprey MV-22
Trong khi quân đội Mỹ đang tung ra những chiếc xe mui trần của họ, các nhà sản xuất xe tăng Armata của Nga đã sử dụng một máy in công nghiệp tại Uralvagonzavod được năm thứ hai. Với sự giúp đỡ của nó, các bộ phận cho xe bọc thép, cũng như các sản phẩm dân dụng, được sản xuất. Nhưng cho đến nay, những bộ phận như vậy chỉ được sử dụng cho các nguyên mẫu, chẳng hạn, chúng được sử dụng trong quá trình chế tạo xe tăng Armata và các cuộc thử nghiệm của nó. Tại Kalashnikov Concern, cũng như tại TsNIITOCHMASH, theo lệnh của quân đội Nga, các nhà thiết kế chế tạo các bộ phận khác nhau của vũ khí nhỏ từ kim loại và chip polymer bằng máy in 3D. Phòng thiết kế dụng cụ Tula được đặt theo tên của Shipunov, CPB nổi tiếng, được biết đến với nhiều loại vũ khí được sản xuất phong phú: từ súng lục đến tên lửa chính xác cao, không hề tụt hậu. Ví dụ, một khẩu súng lục đầy hứa hẹn và một khẩu súng trường tấn công ADS, nhằm thay thế cho lực lượng đặc nhiệm AK74M và APS, được lắp ráp từ các bộ phận nhựa có độ bền cao được in trên máy in. Đối với một số sản phẩm quân sự, CPB đã có thể tạo khuôn mẫu; hiện tại, quá trình lắp ráp nối tiếp các sản phẩm đang được thực hiện.
Trong điều kiện diễn ra cuộc chạy đua vũ trang mới trên thế giới, thời điểm ra mắt các loại vũ khí mới càng trở nên quan trọng. Ví dụ, đối với xe bọc thép, chỉ riêng quá trình tạo ra một mô hình và chuyển nó từ bản vẽ sang nguyên mẫu thường mất một hoặc hai năm. Khi phát triển tàu ngầm, khoảng thời gian này đã dài gấp 2 lần. Alexey Kondratyev, một chuyên gia trong lĩnh vực hải quân cho biết: “Công nghệ in 3D sẽ giảm khoảng thời gian từ vài lần đến vài tháng. - Nhân viên thiết kế sẽ tiết kiệm được thời gian lên bản vẽ khi thiết kế mô hình 3D trên máy tính và làm ngay nguyên mẫu của bộ phận mong muốn. Thông thường, các phần được làm lại có tính đến các bài kiểm tra đã thực hiện và đang trong quá trình sửa đổi. Trong trường hợp này, bạn có thể tháo cụm thay thế cho bộ phận và kiểm tra tất cả các đặc tính cơ học, cách các bộ phận tương tác với nhau. Cuối cùng, thời gian tạo mẫu sẽ cho phép các nhà thiết kế giảm tổng thời gian để mẫu hoàn thiện đầu tiên bước vào giai đoạn thử nghiệm. Ngày nay, phải mất khoảng 15-20 năm để tạo ra một tàu ngầm hạt nhân thế hệ mới: từ bản phác thảo đến chiếc vít cuối cùng trong quá trình lắp ráp. Với sự phát triển hơn nữa của in ba chiều công nghiệp và việc ra mắt sản xuất hàng loạt các bộ phận theo cách này, khung thời gian có thể giảm ít nhất 1,5-2 lần."
Theo các chuyên gia, các công nghệ hiện đại hiện nay chỉ còn cách một đến hai năm nữa là có thể sản xuất hàng loạt các bộ phận bằng titan trên máy in 3D. Có thể nói rằng đến cuối năm 2020, các đại diện quân đội tại các doanh nghiệp của khu liên hợp công nghiệp-quân sự sẽ chấp nhận các thiết bị sẽ được lắp ráp 30-50% bằng công nghệ in 3D. Đồng thời, tầm quan trọng lớn nhất đối với các nhà khoa học là việc tạo ra các bộ phận bằng gốm trên máy in 3D, được phân biệt bởi độ bền cao, nhẹ và các đặc tính che chắn nhiệt. Vật liệu này được sử dụng rất rộng rãi trong các ngành công nghiệp hàng không và vũ trụ, nhưng nó có thể được sử dụng với khối lượng lớn hơn nữa. Ví dụ, việc tạo ra động cơ gốm trên máy in 3D mở ra chân trời cho việc tạo ra máy bay siêu thanh. Với động cơ như vậy, một chiếc máy bay chở khách có thể bay từ Vladivostok đến Berlin trong vài giờ.
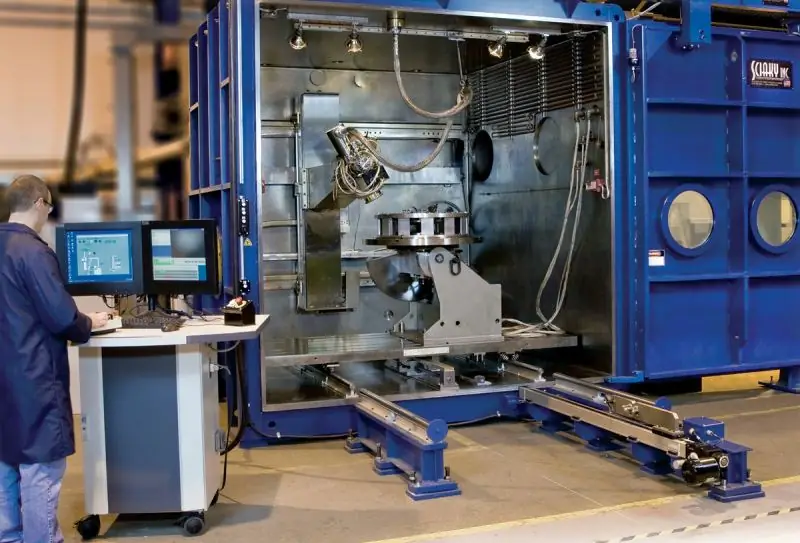
Cũng có thông tin cho rằng các nhà khoa học Mỹ đã phát minh ra một công thức nhựa đặc biệt để in trong máy in 3D. Giá trị của công thức này nằm ở độ bền cao của các vật liệu thu được từ nó. Ví dụ, một vật liệu như vậy có thể chịu được nhiệt độ tới hạn vượt quá 1700 độ C, cao hơn gấp mười lần so với khả năng chịu đựng của nhiều vật liệu hiện đại. Stephanie Tompkins, Giám đốc Khoa học Nghiên cứu Quốc phòng Tiên tiến, ước tính rằng các vật liệu mới được tạo ra bằng máy in 3D sẽ có sự kết hợp độc đáo của các đặc điểm và tính chất chưa từng thấy trước đây. Nhờ công nghệ mới, Tompkins cho biết chúng tôi sẽ có thể sản xuất một bộ phận bền, vừa nhẹ vừa lớn. Các nhà khoa học tin rằng việc sản xuất các bộ phận bằng gốm trên máy in 3D sẽ có nghĩa là một bước đột phá khoa học, bao gồm cả việc sản xuất các sản phẩm dân dụng.
Vệ tinh 3D đầu tiên của Nga
Hiện tại, công nghệ in 3D đã sản xuất thành công các bộ phận trực tiếp trên các trạm vũ trụ. Nhưng các chuyên gia trong nước đã quyết định đi xa hơn nữa, họ ngay lập tức quyết định tạo ra một vệ tinh siêu nhỏ bằng máy in 3D. Tập đoàn Tên lửa và Không gian Energia đã tạo ra một vệ tinh, thân, giá đỡ và một số bộ phận khác của chúng được in 3D. Đồng thời, một điều quan trọng làm rõ là microsatellite được tạo ra bởi các kỹ sư Energia cùng với các sinh viên của Đại học Bách khoa Tomsk (TPU). Vệ tinh máy in đầu tiên có tên đầy đủ là "Tomsk-TPU-120" (số 120 trong tên để vinh danh kỷ niệm 120 năm thành lập trường, được tổ chức vào tháng 5 năm 2016). Nó được phóng thành công vào không gian vào mùa xuân năm 2016 cùng với tàu vũ trụ Progress MS-02, vệ tinh được đưa lên ISS và sau đó được phóng lên vũ trụ. Đây là vệ tinh 3D đầu tiên và duy nhất trên thế giới.
Vệ tinh do sinh viên TPU tạo ra thuộc lớp vệ tinh nano (CubSat). Nó có các kích thước sau 300x100x100 mm. Vệ tinh này là tàu vũ trụ đầu tiên trên thế giới có cơ thể được in 3D. Trong tương lai, công nghệ này có thể trở thành một bước đột phá thực sự trong việc tạo ra các vệ tinh nhỏ, cũng như giúp việc sử dụng chúng trở nên phổ biến và dễ tiếp cận hơn. Thiết kế của tàu vũ trụ được phát triển tại Trung tâm Khoa học và Giáo dục TPU "Công nghệ Sản xuất Hiện đại". Các vật liệu chế tạo vệ tinh được tạo ra bởi các nhà khoa học từ Đại học Bách khoa Tomsk và Viện Vật lý Sức mạnh và Khoa học Vật liệu thuộc Chi nhánh Siberi của Viện Hàn lâm Khoa học Nga. Mục đích chính của vệ tinh là thử nghiệm các công nghệ mới của khoa học vật liệu không gian; nó sẽ giúp các nhà khoa học Nga kiểm tra một số bước phát triển của trường đại học Tomsk và các đối tác của nó.
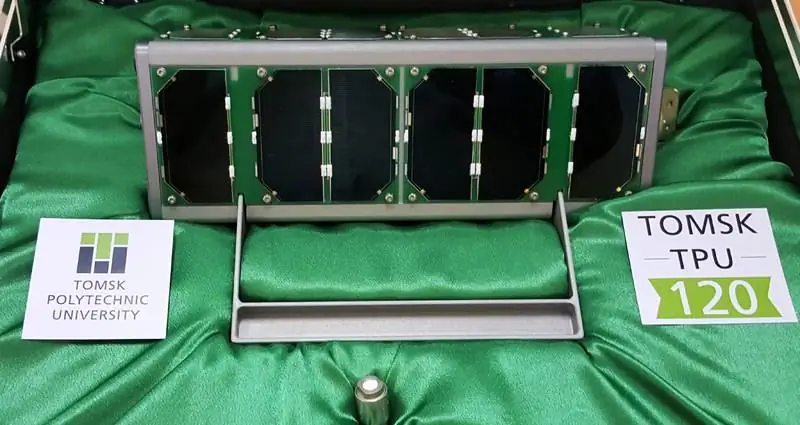
Theo dịch vụ báo chí của trường đại học, việc phóng vệ tinh nano Tomsk-TPU-120 đã được lên kế hoạch thực hiện trong chuyến đi bộ từ ISS. Vệ tinh này là một vệ tinh khá nhỏ gọn, nhưng đồng thời là một tàu vũ trụ chính thức, được trang bị pin, tấm pin mặt trời, thiết bị vô tuyến trên tàu và các thiết bị khác. Nhưng đặc điểm chính của nó là phần thân của nó được in 3D.
Nhiều cảm biến khác nhau của vệ tinh nano sẽ ghi lại nhiệt độ trên bo mạch, trên pin và bo mạch, và các thông số của linh kiện điện tử. Tất cả thông tin này sau đó sẽ được truyền trực tuyến đến Earth. Dựa trên thông tin này, các nhà khoa học Nga sẽ có thể phân tích trạng thái của các vật liệu vệ tinh và quyết định liệu họ có sử dụng chúng để phát triển và chế tạo tàu vũ trụ trong tương lai hay không. Cần lưu ý rằng một khía cạnh quan trọng của sự phát triển tàu vũ trụ nhỏ cũng là đào tạo nhân lực mới cho ngành. Ngày nay, sinh viên và giáo viên của Đại học Bách khoa Tomsk, bằng chính bàn tay của mình, phát triển, chế tạo và cải tiến thiết kế của tất cả các loại tàu vũ trụ nhỏ, đồng thời đạt được không chỉ kiến thức cơ bản chất lượng cao mà còn cả các kỹ năng thực hành cần thiết. Đây là những gì làm cho sinh viên tốt nghiệp của cơ sở giáo dục này trở thành chuyên gia duy nhất trong tương lai.
Các kế hoạch tương lai của các nhà khoa học Nga và đại diện ngành bao gồm việc tạo ra một loạt các vệ tinh của trường đại học. “Hôm nay chúng ta đang nói về nhu cầu thúc đẩy sinh viên của mình nghiên cứu mọi thứ, bằng cách này hay cách khác, được kết nối với không gian - đó có thể là năng lượng, vật liệu và việc tạo ra các động cơ thế hệ mới, v.v. Chúng tôi đã thảo luận trước đó rằng mối quan tâm đến không gian trong nước đã giảm đi phần nào, nhưng nó có thể được hồi sinh. Để làm được điều này, cần phải bắt đầu không phải ngay từ băng ghế của học sinh, mà bắt đầu từ trường học. Vì vậy, chúng tôi đã bắt tay vào con đường phát triển và sản xuất CubeSat - vệ tinh nhỏ”, - dịch vụ báo chí của Học viện Bách khoa Tomsk ghi nhận với hiệu trưởng của cơ sở giáo dục đại học này, Peter Chubik.