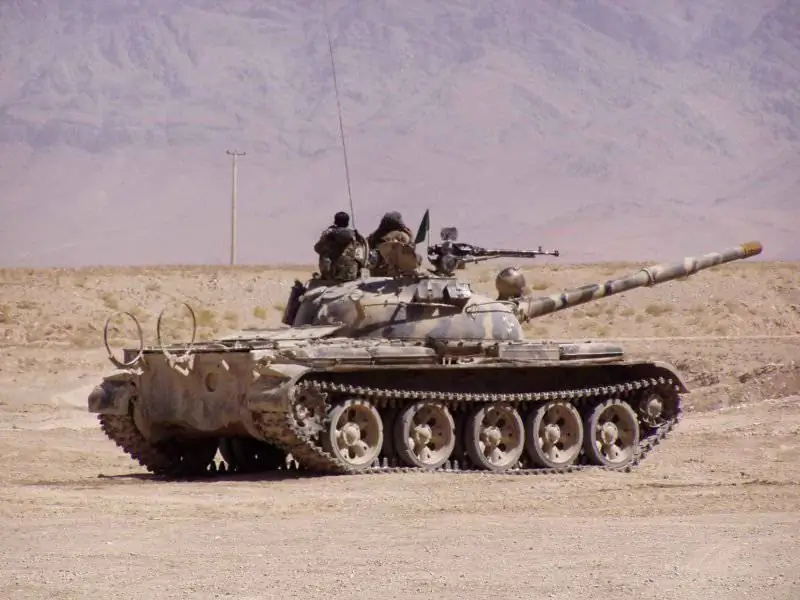
Năm 1955, chính phủ quyết định thành lập một phòng thiết kế kỹ thuật diesel đặc biệt tại Nhà máy Kỹ thuật Giao thông vận tải Kharkov và tạo ra một động cơ diesel cho xe tăng mới. Giáo sư A. D. Charomsky được bổ nhiệm làm trưởng phòng thiết kế.

Việc lựa chọn phương án thiết kế động cơ diesel tương lai được quyết định chủ yếu bởi kinh nghiệm làm việc trên động cơ diesel 2 thì OND TsIAM và động cơ U-305, cũng như mong muốn đáp ứng các yêu cầu của các nhà thiết kế của T -64 xe tăng, được phát triển tại nhà máy này dưới sự lãnh đạo của nhà thiết kế chính AA … Morozov: để đảm bảo kích thước tối thiểu của động cơ diesel, đặc biệt là về chiều cao, kết hợp với khả năng đặt nó trong thùng ở vị trí nằm ngang giữa các hộp số hành tinh trên tàu. Một sơ đồ động cơ diesel hai kỳ được lựa chọn với sự sắp xếp theo chiều ngang của năm xi lanh với các piston chuyển động ngược chiều nhau. Người ta quyết định chế tạo một động cơ có khả năng lạm phát và sử dụng năng lượng khí thải trong tuabin.
Cơ sở lý luận đằng sau việc lựa chọn động cơ diesel 2 kỳ là gì?
Trước đó, vào những năm 1920-1930, việc chế tạo động cơ diesel 2 thì cho các phương tiện hàng không và mặt đất đã bị đình trệ do nhiều vấn đề chưa giải quyết được với trình độ kiến thức, kinh nghiệm và năng lực của ngành công nghiệp trong nước được tích lũy bởi thời gian đó.
Việc tìm hiểu và nghiên cứu động cơ diesel 2 kỳ của một số hãng nước ngoài đã đưa ra kết luận về khó khăn đáng kể trong việc làm chủ chúng trong sản xuất. Vì vậy, ví dụ, một nghiên cứu của Viện Động cơ Hàng không Trung ương (CIAM) vào những năm 30 về động cơ diesel Jumo-4 do Hugo Juneckers thiết kế đã chỉ ra những vấn đề nghiêm trọng liên quan đến sự phát triển của động cơ như vậy trong quá trình sản xuất động cơ như vậy trong nước. ngành của thời kỳ đó. Cũng được biết rằng Anh và Nhật Bản, đã mua giấy phép cho động cơ diesel này, đã gặp phải những thất bại trong quá trình phát triển động cơ Junkers. Đồng thời, vào những năm 30 và 40, công trình nghiên cứu về động cơ điêzen 2 kỳ đã được thực hiện ở nước ta và các mẫu thử nghiệm của động cơ này đã được chế tạo. Vai trò chủ đạo trong các công việc này thuộc về các chuyên gia CIAM và đặc biệt là Vụ Động cơ Dầu (OND). CIAM đã thiết kế và sản xuất các mẫu động cơ diesel 2 thì với nhiều kích thước khác nhau: OH-2 (12/16, 3), OH-16 (14/11), OH-17 (18/20), OH-4 (8 / 9) và một số động cơ nguyên bản khác.
Trong số đó có động cơ FED-8, được thiết kế dưới sự hướng dẫn của các nhà khoa học động cơ lỗi lạc B. S. Stechkin, N. R. Briling, A. A. Bessonov. Đó là động cơ diesel máy bay 2 thì 16 xi-lanh hình chữ X với phân phối khí van-pít-tông, với kích thước 18/23, phát triển công suất 1470 kW (2000 mã lực). Một trong những đại diện của động cơ diesel 2 kỳ có tăng áp là động cơ diesel turbo-piston 6 xi-lanh hình ngôi sao với công suất 147 … 220 kW (200 … 300 mã lực) được sản xuất tại CIAM dưới sự lãnh đạo của BS Stechkin. Công suất của tuabin khí được truyền tới trục khuỷu thông qua một hộp số phù hợp.
Quyết định được đưa ra sau đó khi tạo ra động cơ FED-8 xét về mặt ý tưởng và sơ đồ thiết kế sau đó thể hiện một bước tiến quan trọng. Tuy nhiên, quá trình làm việc và đặc biệt là quá trình trao đổi khí ở mức điều áp cao và thổi vòng vẫn chưa được thực hiện sơ bộ. Do đó, động cơ diesel FED-8 không được phát triển thêm và vào năm 1937, công việc chế tạo nó đã bị dừng lại.
Sau chiến tranh, tài liệu kỹ thuật của Đức trở thành tài sản của Liên Xô. Cô ấy rơi vào A. D. Charomsky với tư cách là một nhà phát triển động cơ máy bay, và anh ấy quan tâm đến chiếc vali của Junkers.
Vali Junkers - một loạt máy bay động cơ hai thì turbo-piston Jumo 205 với các piston chuyển động ngược chiều được tạo ra vào đầu những năm 30 của thế kỷ XX. Các đặc điểm của động cơ Jumo 205-C như sau: 6 xi-lanh, 600 mã lực. hành trình 2 x 160 mm, dung tích 16,62 lít, tỷ số nén 17: 1, tại 2.200 vòng / phút
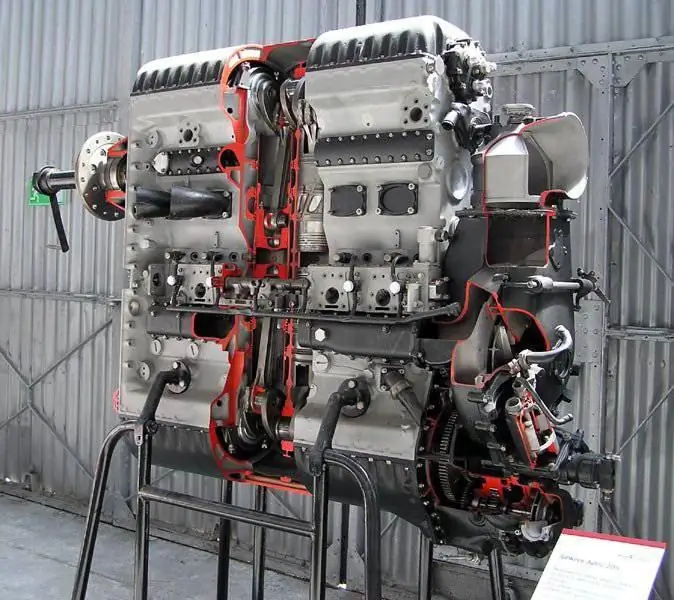
Động cơ Jumo 205
Trong chiến tranh, khoảng 900 động cơ đã được sản xuất, được sử dụng thành công trên các thủy phi cơ Do-18, Do-27, và sau này là các xuồng cao tốc. Ngay sau khi Chiến tranh thế giới thứ hai kết thúc vào năm 1949, người ta đã quyết định lắp đặt những động cơ như vậy trên các tàu tuần tra của Đông Đức, vốn được phục vụ cho đến những năm 60.
Trên cơ sở những phát triển này, AD Charomsky vào năm 1947 ở Liên Xô đã chế tạo ra động cơ diesel cho máy bay hai thì M-305 và một khoang xi-lanh của động cơ U-305 này. Động cơ diesel này đã phát triển công suất 7350 kW (10.000 mã lực) với trọng lượng riêng thấp (0,5 kg / h.p.) và mức tiêu thụ nhiên liệu riêng thấp -190 g / kWh (140 g / h.p.h). Một cách sắp xếp hình chữ X gồm 28 hình trụ (4 khối 7 xi lanh) đã được thông qua. Chiều của động cơ được chọn bằng 12/12. Khả năng tăng cao được cung cấp bởi một bộ tăng áp được kết nối cơ học với trục động cơ diesel. Để kiểm tra các đặc điểm chính của dự án M-305, để tìm ra quy trình làm việc và thiết kế các bộ phận, một mô hình thử nghiệm của động cơ đã được chế tạo, có chỉ số U-305. G. V. Orlova, N. I. Rudakov, L. V. Ustinova, N. S. Zolotarev, S. M. Shifrin, N. S. Sobolev, cũng như các nhà công nghệ và công nhân của nhà máy thí điểm CIAM và phân xưởng OND.
Dự án chế tạo động cơ diesel cho máy bay cỡ lớn M-305 đã không được thực hiện, vì công việc của CIAM, giống như toàn bộ ngành hàng không của đất nước, vào thời điểm đó đã tập trung vào phát triển động cơ phản lực và động cơ phản lực cánh quạt và nhu cầu về một Động cơ diesel 10.000 mã lực cho ngành hàng không đã biến mất.
Các chỉ số cao thu được trên động cơ diesel U-305: công suất động cơ lít 99 kW / l (135 mã lực / l), công suất lít từ một xi lanh gần 220 kW (300 mã lực) ở áp suất tăng 0,35 MPa; tốc độ quay cao (3500 vòng / phút) và dữ liệu từ một số thử nghiệm dài hạn thành công của động cơ - đã khẳng định khả năng tạo ra một động cơ diesel 2 kỳ cỡ nhỏ hiệu quả cho mục đích vận tải với các chỉ số và cấu trúc tương tự.
Năm 1952, phòng thí nghiệm số 7 (OND cũ) của CIAM được chuyển đổi theo quyết định của chính phủ thành Phòng thí nghiệm Nghiên cứu Động cơ (NILD) với sự trực thuộc của Bộ Giao thông Vận tải. Một nhóm nhân viên sáng kiến - các chuyên gia có trình độ cao về động cơ diesel (G. V. Orlova, N. I. Rudakov, S. M. Shifrin, v.v.), do Giáo sư A. D. Charomsky đứng đầu, đã ở NILD (sau này - NIID) về tinh chỉnh và nghiên cứu động cơ 2 thì U-305.
Diesel 5TDF
Năm 1954, A. D. Charomsky đưa ra đề xuất với chính phủ về việc tạo ra động cơ diesel cho xe tăng 2 kỳ. Đề xuất này trùng hợp với yêu cầu của nhà thiết kế chính về xe tăng mới A. A. Morozov và A. D. Charomsky được bổ nhiệm làm thiết kế trưởng của nhà máy. V. Malyshev ở Kharkov.
Vì văn phòng thiết kế động cơ xe tăng của nhà máy này chủ yếu vẫn ở Chelyabinsk, A. D. Charomsky phải thành lập một văn phòng thiết kế mới, tạo cơ sở thử nghiệm, thiết lập sản xuất thử nghiệm và sản xuất hàng loạt, đồng thời phát triển công nghệ mà nhà máy không có. Công việc bắt đầu với việc sản xuất một đơn vị xi-lanh đơn (OTsU), tương tự như động cơ U-305. Tại OTsU, các yếu tố và quy trình của động cơ diesel xe tăng cỡ lớn trong tương lai đã được nghiên cứu.
Những người tham gia chính trong công việc này là A. D. Charomsky, G. A. Volkov, L. L. Golinets, B. M. Kugel, M. A., Meksin, I. L. Rovensky, và những người khác.
Năm 1955, các nhân viên của NILD tham gia công việc thiết kế tại nhà máy diesel: G. V. Orlova, N. I. Rudakov, V. G. Lavrov, I. S. Elperin, I. K. Lagovsky và các chuyên gia NILD khác L. M. Belinsky, LI Pugachev, LSRoninson, SM Shifrin thực hiện công việc thử nghiệm tại OTsU tại Nhà máy Kỹ thuật Giao thông vận tải Kharkov. Đây là cách mà 4TPD của Liên Xô xuất hiện. Đó là một động cơ hoạt động, nhưng có một nhược điểm - công suất chỉ hơn 400 mã lực, không đủ cho một chiếc xe tăng. Charomsky đặt một xi lanh khác vào và nhận được 5TD.
Sự ra đời của một xi lanh bổ sung đã làm thay đổi nghiêm trọng tính năng động của động cơ. Sự mất cân bằng phát sinh gây ra dao động xoắn cực mạnh trong hệ thống. Các lực lượng khoa học hàng đầu của Leningrad (VNII-100), Moscow (NIID) và Kharkov (KhPI) đang tham gia vào giải pháp của nó. 5TDF đã được đưa vào điều kiện THỰC NGHIỆM, bằng cách thử và sai.
Kích thước của động cơ này được chọn bằng 12/12, tức là giống như trên động cơ U-305 và OTsU. Để cải thiện phản ứng tiết lưu của động cơ diesel, người ta quyết định kết nối cơ khí tuabin và máy nén với trục khuỷu.
Diesel 5TD có các tính năng sau:
- công suất cao - 426 kW (580 mã lực) với kích thước tổng thể tương đối nhỏ;
- tăng tốc độ - 3000 vòng / phút;
- hiệu quả của việc điều áp và sử dụng năng lượng khí thải;
- chiều cao thấp (dưới 700 mm);
- giảm 30-35% sự truyền nhiệt so với động cơ diesel 4 kỳ (hút khí tự nhiên) hiện có, và do đó, yêu cầu thể tích nhỏ hơn cho hệ thống làm mát của nhà máy điện;
- hiệu suất nhiên liệu đạt yêu cầu và khả năng vận hành động cơ không chỉ bằng nhiên liệu điêzen, mà còn bằng dầu hỏa, xăng và các hỗn hợp khác nhau của chúng;
- công suất cất cánh từ cả hai đầu và chiều dài tương đối nhỏ của nó, giúp có thể lắp ráp thùng MTO với cách bố trí ngang của động cơ diesel giữa hai hộp số trên bo mạch với thể tích chiếm chỗ nhỏ hơn nhiều so với cách bố trí dọc của động cơ và hộp số trung tâm;
- bố trí thành công các thiết bị như máy nén khí áp suất cao với hệ thống riêng, máy phát điện khởi động, v.v.
Vẫn giữ nguyên cách bố trí ngang của động cơ với công suất phát hai chiều và hai hộp số hành tinh nằm ở hai bên động cơ, các nhà thiết kế đã chuyển sang những chỗ trống ở hai bên động cơ, song song với hộp số., máy nén và tuabin khí, trước đây được gắn trong 4TD trên đầu khối động cơ. Cách bố trí mới giúp giảm một nửa khối lượng của MTO so với xe tăng T-54, và các thành phần truyền thống như hộp số trung tâm, hộp số, ly hợp chính, cơ cấu xoay hành tinh, hệ thống truyền động và phanh cuối cùng đã bị loại trừ khỏi nó. Như đã đề cập sau đó trong báo cáo GBTU, loại hộp số mới tiết kiệm được 750 kg khối lượng và bao gồm 150 bộ phận được gia công thay vì 500 bộ trước đó.
Tất cả các hệ thống bảo dưỡng động cơ đều được lồng vào nhau phía trên động cơ diesel, tạo thành "tầng thứ hai" của MTO, sơ đồ này được đặt tên là "hai tầng".
Hiệu suất cao của động cơ 5TD đòi hỏi phải sử dụng một số giải pháp cơ bản mới và vật liệu đặc biệt trong thiết kế của nó. Ví dụ, pít-tông cho động cơ diesel này được sản xuất bằng cách sử dụng một tấm đệm nhiệt và một miếng đệm.
Vòng piston đầu tiên là một vòng lửa kiểu môi liên tục. Các xi lanh được làm bằng thép, mạ chrome.
Khả năng vận hành động cơ với áp suất chớp cháy cao được cung cấp bởi mạch điện của động cơ với các bu lông thép hỗ trợ, một khối nhôm đúc không tải khỏi tác động của lực khí và không có khớp khí. Việc cải thiện quá trình làm sạch và nạp đầy xi lanh (và đây là vấn đề đối với tất cả các động cơ diesel 2 kỳ) đã được tạo điều kiện ở một mức độ nhất định nhờ sơ đồ động lực khí sử dụng động năng của khí thải và hiệu ứng phụt ra.
Hệ thống hình thành hỗn hợp phản lực-xoáy, trong đó bản chất và hướng của các tia nhiên liệu được phối hợp với hướng chuyển động của không khí, đảm bảo hỗn hợp nhiên liệu-không khí hỗn hợp hiệu quả, góp phần cải thiện quá trình truyền nhiệt và khối lượng.
Hình dạng được lựa chọn đặc biệt của buồng đốt cũng giúp cải thiện quá trình trộn và đốt. Các nắp ổ trục chính được kéo cùng với cacte bằng các bu lông trợ lực bằng thép, chịu tải trọng từ các lực khí tác dụng lên piston.
Một tấm có tuabin và một máy bơm nước được gắn vào một đầu của khối cacte, còn một tấm của hộp số chính và bao gồm các ổ đĩa cho bộ tăng áp, bộ điều chỉnh, cảm biến tốc độ kế, máy nén áp suất cao và bộ phân phối khí được gắn vào phía đối diện kết thúc.
Vào tháng 1 năm 1957, nguyên mẫu đầu tiên của động cơ diesel cho xe tăng 5TD đã được chuẩn bị cho các cuộc thử nghiệm trên băng ghế dự bị. Khi kết thúc các thử nghiệm trên băng ghế dự bị, chiếc 5TD trong cùng năm đã được chuyển sang thử nghiệm vật thể (biển) trong một xe tăng thử nghiệm "Object 430", và đến tháng 5 năm 1958, đã vượt qua các thử nghiệm cấp Tiểu bang với điểm số tốt.
Tuy nhiên, họ đã quyết định không chuyển động cơ diesel 5TD sang sản xuất hàng loạt. Lý do một lần nữa là sự thay đổi trong yêu cầu của quân đội đối với xe tăng mới, điều này một lần nữa đòi hỏi sự gia tăng sức mạnh. Tính đến các chỉ tiêu kinh tế kỹ thuật rất cao của động cơ 5TD và trữ lượng vốn có trong nó (cũng đã được chứng minh qua các cuộc thử nghiệm), một nhà máy điện mới có công suất khoảng 700 mã lực. quyết định tạo ra trên cơ sở của nó.
Việc tạo ra một động cơ ban đầu như vậy cho nhà máy kỹ thuật giao thông Kharkov đòi hỏi phải chế tạo các thiết bị công nghệ quan trọng, một số lượng lớn các nguyên mẫu của động cơ diesel và các thử nghiệm lặp lại trong thời gian dài. Cần lưu ý rằng bộ phận thiết kế của nhà máy sau này trở thành Cục Cơ khí Thiết kế Kharkov (KHKBD), và việc sản xuất động cơ thực tế được tạo ra từ đầu sau chiến tranh.
Đồng thời với việc thiết kế động cơ diesel, một tổ hợp lớn các gian hàng thí nghiệm và nhiều hệ thống lắp đặt khác nhau (24 đơn vị) đã được tạo ra tại nhà máy để kiểm tra các yếu tố trong thiết kế và quy trình làm việc của nó. Điều này đã giúp ích rất nhiều cho việc kiểm tra và tìm ra thiết kế của các bộ phận như bộ tăng áp, tuabin, máy bơm nhiên liệu, ống xả, máy ly tâm, máy bơm nước và dầu, cacte khối, v.v., tuy nhiên, sự phát triển của chúng vẫn tiếp tục phát triển hơn nữa.
Năm 1959, theo yêu cầu của nhà thiết kế chính của chiếc xe tăng mới (AA Morozov), người mà động cơ diesel này được thiết kế cho mục đích này, nó được cho là cần thiết phải tăng công suất của nó từ 426 kW (580 hp) lên 515 kW (700 hp).). Phiên bản cưỡng bức của động cơ được đặt tên là 5TDF.
Bằng cách tăng tốc độ của máy nén tăng áp, công suất lít của động cơ đã được tăng lên. Tuy nhiên, kết quả của việc buộc động cơ diesel, các vấn đề mới đã xuất hiện, chủ yếu là về độ tin cậy của các bộ phận và cụm lắp ráp.
Các nhà thiết kế của KhKBD, NIID, VNIITransmash, các nhà công nghệ của nhà máy và viện VNITI và TsNITI (từ năm 1965) đã thực hiện rất nhiều công việc tính toán, nghiên cứu, thiết kế và công nghệ để đạt được độ tin cậy và thời gian hoạt động cần thiết của động cơ diesel 5TDF.
Những vấn đề khó khăn nhất hóa ra là vấn đề tăng độ tin cậy của nhóm pít-tông, thiết bị nhiên liệu và bộ tăng áp. Mọi cải tiến, thậm chí không đáng kể chỉ được đưa ra do kết quả của toàn bộ các biện pháp thiết kế, công nghệ, tổ chức (sản xuất).
Lô động cơ diesel 5TDF đầu tiên được đặc trưng bởi sự không ổn định lớn về chất lượng của các bộ phận và cụm lắp ráp. Một bộ phận nhất định của động cơ diesel từ loạt (lô) được sản xuất đã tích lũy thời gian vận hành bảo hành đã thiết lập (300 giờ). Đồng thời, một phần đáng kể động cơ đã được đưa ra khỏi khán đài trước thời gian vận hành bảo hành do một số khiếm khuyết nhất định.
Đặc thù của động cơ diesel 2 kỳ tốc độ cao nằm ở hệ thống trao đổi khí phức tạp hơn so với động cơ 4 kỳ, lượng khí tiêu thụ tăng lên, nhóm pít-tông tải nhiệt cao hơn. Do đó, độ cứng và khả năng chống rung của kết cấu, tuân thủ nghiêm ngặt hơn về hình dạng hình học của một số bộ phận, tính chống co giật cao và khả năng chống mài mòn của xi lanh, khả năng chịu nhiệt và độ bền cơ học của piston, cung cấp và loại bỏ chất bôi trơn xi lanh cẩn thận và yêu cầu cải thiện chất lượng bề mặt cọ xát. Để tính đến những đặc điểm cụ thể này của động cơ 2 kỳ, cần phải giải quyết những vấn đề phức tạp về thiết kế và công nghệ.
Một trong những bộ phận quan trọng nhất cung cấp sự phân phối khí chính xác và bảo vệ các vòng đệm của piston khỏi quá nhiệt là vòng lửa kiểu vòng bít thành mỏng bằng thép có ren với lớp phủ chống ma sát đặc biệt. Trong quá trình cải tiến động cơ diesel 5TDF, vấn đề về khả năng vận hành của vòng này đã trở thành một trong những vấn đề chính. Trong quá trình tinh chỉnh, lâu ngày xảy ra hiện tượng sứt mẻ và vỡ vòng lửa do mặt phẳng đỡ của chúng bị biến dạng, cấu hình của cả bản thân vòng và thân piston không đạt, lớp mạ crom không đạt yêu cầu, bôi trơn không đủ., cung cấp nhiên liệu không đồng đều bởi các vòi phun, đóng cặn và lắng đọng muối hình thành trên lớp lót pít-tông, cũng như do mài mòn bụi liên quan đến mức độ làm sạch không đủ của không khí hút vào động cơ.
Chỉ là kết quả của quá trình làm việc lâu dài và chăm chỉ của nhiều chuyên gia của nhà máy và viện nghiên cứu và công nghệ, khi cấu hình của piston và vòng lửa được cải tiến, công nghệ chế tạo được cải tiến, các chi tiết của thiết bị nhiên liệu được cải tiến, khả năng bôi trơn được cải thiện, việc sử dụng các lớp phủ chống ma sát hiệu quả hơn, cũng như cải tiến các lỗi của hệ thống làm sạch không khí liên quan đến hoạt động của vòng lửa trên thực tế đã được loại bỏ.
Ví dụ, sự cố của vòng piston hình thang đã được loại bỏ bằng cách giảm khe hở dọc trục giữa vòng và rãnh piston, cải tiến vật liệu, thay đổi cấu hình của mặt cắt ngang của vòng (chuyển từ hình thang sang hình chữ nhật) và cải tiến công nghệ để sản xuất nhẫn. Các vết nứt của bu lông lót pít tông đã được sửa chữa bằng cách vặn lại ren và khóa, thắt chặt các điều khiển sản xuất, thắt chặt các giới hạn mô-men xoắn và sử dụng vật liệu bu lông cải tiến.
Sự ổn định của việc tiêu thụ dầu đạt được bằng cách tăng độ cứng của xi lanh, giảm kích thước của các vết cắt ở đầu xi lanh, thắt chặt kiểm soát trong sản xuất vòng thu dầu.
Bằng cách tinh chỉnh các yếu tố của thiết bị nhiên liệu và cải thiện trao đổi khí, một số cải thiện về hiệu suất nhiên liệu và giảm áp suất chớp cháy tối đa đã đạt được.
Bằng cách cải thiện chất lượng cao su được sử dụng và hợp lý hóa khe hở giữa xi lanh và khối, các trường hợp rò rỉ chất làm mát qua các vòng đệm cao su đã được loại bỏ.
Liên quan đến sự gia tăng đáng kể tỷ số truyền từ trục khuỷu đến bộ siêu nạp, một số động cơ diesel 5TDF đã bộc lộ các khuyết tật như trượt và mòn đĩa ly hợp ma sát, hỏng bánh xe tăng áp và hỏng vòng bi, không có mặt trên Động cơ diesel 5TD. Để loại bỏ chúng, cần thực hiện các biện pháp như chọn độ chặt tối ưu của gói đĩa ly hợp ma sát, tăng số lượng đĩa trong gói, loại bỏ các bộ phận tập trung ứng suất trong bánh công tác tăng áp, làm rung bánh xe, tăng đặc tính giảm xóc của hỗ trợ và lựa chọn vòng bi tốt hơn. Điều này làm cho nó có thể loại bỏ các khiếm khuyết do ép buộc động cơ diesel về mặt công suất.
Sự gia tăng độ tin cậy và thời gian hoạt động của động cơ diesel 5TDF đã góp phần lớn vào việc sử dụng các loại dầu chất lượng cao hơn với các chất phụ gia đặc biệt.
Tại gian hàng của VNIITransmash, với sự tham gia của các nhân viên KKBD và NIID, một số lượng lớn các nghiên cứu đã được thực hiện về hoạt động của động cơ diesel 5TDF trong điều kiện khí nạp thực sự bẩn. Cuối cùng, họ đã đạt đến đỉnh điểm là một thử nghiệm thành công về độ "bụi" của động cơ trong hơn 500 giờ hoạt động. Điều này khẳng định mức độ phát triển cao của nhóm xi-lanh-pít-tông của động cơ diesel và hệ thống làm sạch không khí.
Song song với việc tinh chỉnh bản thân động cơ diesel, nó đã được thử nghiệm nhiều lần cùng với hệ thống nhà máy điện. Đồng thời, các hệ thống đang được cải thiện, vấn đề kết nối với nhau và hoạt động đáng tin cậy của chúng trong bể đang được giải quyết.
L. L. Golinets là nhà thiết kế chính của KHKBD trong giai đoạn quyết định tinh chỉnh động cơ diesel 5TDF. Cựu thiết kế trưởng A. D. Charomsky đã nghỉ hưu và tiếp tục tham gia vào công việc tinh chỉnh với tư cách là nhà tư vấn.
Việc phát triển sản xuất nối tiếp động cơ diesel 5TDF trong các phân xưởng mới, có mục đích của nhà máy, với đội ngũ cán bộ công nhân, kỹ sư mới nghiên cứu về động cơ này đã gây nhiều khó khăn, cần có sự tham gia của các chuyên gia từ các tổ chức khác.
Cho đến năm 1965, động cơ 5TDF được sản xuất theo từng loạt (lô) riêng biệt. Mỗi loạt tiếp theo bao gồm một số biện pháp được phát triển và thử nghiệm tại khán đài, loại bỏ các khuyết tật được xác định trong quá trình thử nghiệm và trong quá trình vận hành thử nghiệm trong quân đội.
Tuy nhiên, thời gian hoạt động thực tế của động cơ không vượt quá 100 giờ.
Một bước đột phá đáng kể trong việc nâng cao độ tin cậy của động cơ diesel đã diễn ra vào đầu năm 1965. Vào thời điểm này, một số lượng lớn thay đổi đã được thực hiện đối với thiết kế và công nghệ sản xuất của nó. Được đưa vào sản xuất, những thay đổi này giúp tăng thời gian hoạt động của loạt động cơ tiếp theo lên đến 300 giờ. Các thử nghiệm chạy trong thời gian dài đối với các xe tăng có động cơ thuộc dòng này đã khẳng định độ tin cậy của động cơ diesel tăng lên đáng kể: tất cả các động cơ trong các thử nghiệm này hoạt động 300 giờ, và một số động cơ (có chọn lọc), tiếp tục thử nghiệm, mỗi động cơ hoạt động 400 … 500 giờ.
Năm 1965, một lô lắp đặt động cơ diesel cuối cùng đã được xuất xưởng theo tài liệu bản vẽ kỹ thuật và công nghệ đã được hiệu chỉnh để sản xuất hàng loạt. Tổng cộng 200 động cơ nối tiếp đã được sản xuất vào năm 1965. Sự gia tăng sản lượng bắt đầu, đạt đỉnh vào năm 1980. Vào tháng 9 năm 1966, động cơ diesel 5TDF đã vượt qua các cuộc thử nghiệm giữa các khoa.
Xem xét lịch sử hình thành động cơ diesel 5TDF, cần lưu ý tiến trình phát triển công nghệ của nó như một động cơ hoàn toàn mới cho quá trình sản xuất của nhà máy. Gần như đồng thời với việc sản xuất các nguyên mẫu của động cơ và cải tiến thiết kế của nó, việc phát triển công nghệ và xây dựng các cơ sở sản xuất mới của nhà máy và hoàn thiện chúng với thiết bị đã được thực hiện.
Theo bản vẽ sửa đổi của các mẫu động cơ đầu tiên, vào năm 1960, sự phát triển của công nghệ thiết kế để sản xuất 5TDF bắt đầu, và vào năm 1961, việc sản xuất các tài liệu công nghệ hoạt động bắt đầu. Các đặc điểm thiết kế của động cơ diesel 2 kỳ, việc sử dụng vật liệu mới, độ chính xác cao của từng bộ phận và thành phần của nó đòi hỏi công nghệ phải sử dụng các phương pháp cơ bản mới trong chế biến và thậm chí lắp ráp động cơ. Việc thiết kế các quy trình công nghệ và thiết bị của chúng được thực hiện bởi các dịch vụ công nghệ của nhà máy, đứng đầu là A. I. Isaev, V. D. Dyachenko, V. I. Doschechkin và những người khác, và bởi các nhân viên của các viện công nghệ trong ngành. Các chuyên gia từ Viện Nghiên cứu Vật liệu Trung ương (Giám đốc F. A. Kupriyanov) đã tham gia giải quyết nhiều vấn đề về khoa học vật liệu và luyện kim.
Việc xây dựng các cửa hàng mới để sản xuất động cơ của Nhà máy Cơ khí Giao thông vận tải Kharkov được thực hiện theo dự án của Viện Soyuzmashproekt (kỹ sư trưởng dự án S. I. Shpynov).
Trong thời gian 1964-1967. Việc sản xuất động cơ diesel mới đã được hoàn thành với các thiết bị (đặc biệt là các máy đặc biệt - hơn 100 chiếc), nếu không có thiết bị này thì thực tế không thể tổ chức sản xuất nối tiếp các bộ phận diesel. Đây là những máy doa kim cương và nhiều trục chính để gia công khối, máy tiện và hoàn thiện đặc biệt để gia công trục khuỷu, v.v. Trước khi đưa vào vận hành các phân xưởng và khu vực thử nghiệm mới và gỡ lỗi công nghệ chế tạo cho một số bộ phận chính, cũng như sản xuất các lô lắp đặt và loạt động cơ đầu tiên, các vỏ của đầu máy xe lửa diesel lớn đã được tạm thời tổ chức sản xuất. các trang web.
Việc vận hành thử các công suất chính của sản xuất diesel mới được thực hiện luân phiên trong giai đoạn 1964-1967. Trong các phân xưởng mới, một chu trình sản xuất diesel 5TDF đầy đủ đã được cung cấp, ngoại trừ sản xuất trống tại địa điểm chính của nhà máy.
Khi hình thành các cơ sở sản xuất mới, việc nâng cao trình độ và tổ chức sản xuất đã được chú trọng. Việc sản xuất động cơ diesel được tổ chức theo nguyên tắc dây chuyền và nhóm, có tính đến những thành tựu mới nhất của thời kỳ đó trong lĩnh vực này. Các phương tiện cơ giới hóa và tự động hóa tiên tiến nhất trong quá trình gia công và lắp ráp các bộ phận đã được sử dụng, nhằm đảm bảo việc tạo ra động cơ diesel 5TDF được cơ giới hóa toàn diện.
Trong quá trình hình thành sản xuất, một công việc chung lớn của các nhà công nghệ và nhà thiết kế đã được thực hiện để cải thiện khả năng sản xuất của thiết kế động cơ diesel, trong đó các nhà công nghệ đã đưa ra khoảng sáu nghìn đề xuất cho KHKBD, một phần quan trọng trong số đó được phản ánh trong tài liệu thiết kế của động cơ.
Xét về trình độ kỹ thuật, sản lượng diesel mới vượt đáng kể so với các chỉ tiêu của các doanh nghiệp trong ngành sản xuất sản phẩm tương tự đạt được vào thời điểm đó. Hệ số thiết bị của quá trình sản xuất dầu diesel 5TDF đạt giá trị cao - 6, 22. Chỉ trong 3 năm, hơn 10 nghìn quy trình công nghệ đã được phát triển, hơn 50 nghìn hạng mục thiết bị đã được thiết kế và chế tạo. Một số doanh nghiệp của Hội đồng Kinh tế Kharkov đã tham gia vào việc sản xuất thiết bị và công cụ để hỗ trợ nhà máy Malyshev.
Trong những năm tiếp theo (sau năm 1965), trong quá trình sản xuất hàng loạt động cơ diesel 5TDF, các dịch vụ công nghệ của nhà máy và TsNITI đã tiến hành cải tiến hơn nữa công nghệ nhằm giảm cường độ lao động, nâng cao chất lượng và độ tin cậy của động cơ. Nhân viên của TsNITI (giám đốc Ya. A. Shifrin, kỹ sư trưởng B. N. Surnin) trong thời gian 1967-1970. hơn 4500 đề xuất công nghệ đã được phát triển, giúp giảm cường độ lao động hơn 530 giờ tiêu chuẩn và giảm đáng kể tổn thất do phế liệu trong quá trình sản xuất. Đồng thời, các biện pháp này có thể giảm hơn một nửa số lần thao tác lắp và ghép các bộ phận có chọn lọc. Kết quả của việc thực hiện phức hợp các biện pháp thiết kế và công nghệ là động cơ hoạt động chất lượng cao và đáng tin cậy hơn với thời gian vận hành được đảm bảo là 300 giờ. Nhưng công việc của các nhà công nghệ của nhà máy và TsNITI, cùng với các nhà thiết kế của KHKBD, vẫn tiếp tục. Cần phải tăng thời gian hoạt động của động cơ 5TDF lên 1,5 … 2,0 lần. Nhiệm vụ này cũng được giải quyết. Động cơ diesel cho xe tăng 2 thì 5TDF được cải tiến và đưa vào sản xuất tại Nhà máy Kỹ thuật Giao thông vận tải Kharkov.
Giám đốc nhà máy O. A. Soich, cũng như một số lãnh đạo ngành (D. F. Ustinov, E. P. Shkurko, I. F. Dmitriev, v.v.), đóng một vai trò rất quan trọng trong việc tổ chức sản xuất dầu diesel, liên tục theo dõi tiến độ và sự phát triển của sản xuất dầu diesel, cũng như những người trực tiếp tham gia giải quyết các vấn đề kỹ thuật và tổ chức.
Hệ thống đốt nóng và phun dầu tự động giúp lần đầu tiên (năm 1978) có thể khởi động nguội động cơ diesel xe tăng ở nhiệt độ xuống -20 độ C (từ năm 1984 xuống -25 độ C). Sau đó (năm 1985), với sự trợ giúp của hệ thống PVV (bộ gia nhiệt khí nạp) có thể thực hiện khởi động nguội động cơ diesel 4 kỳ (V-84-1) trên xe tăng T-72, nhưng chỉ tối đa nhiệt độ -20 độ C và không quá 20 độ bắt đầu trong tài nguyên bảo hành.
Quan trọng nhất, 5TDF đã chuyển đổi một cách suôn sẻ sang chất lượng mới trong các động cơ diesel của dòng 6TD (6TD-1… 6TD-4) với dải công suất từ 1000-1500 mã lực.và vượt qua các chất tương tự nước ngoài trong một số thông số cơ bản.
THÔNG TIN VẬN HÀNH ĐỘNG CƠ
Vật liệu vận hành ứng dụng
Loại nhiên liệu chính để cung cấp năng lượng cho động cơ là nhiên liệu cho động cơ diesel tốc độ cao GOST 4749-73:
ở nhiệt độ môi trường không thấp hơn + 5 ° С - Nhãn hiệu DL;
ở nhiệt độ môi trường từ +5 đến -30 ° С - Nhãn hiệu DZ;
ở nhiệt độ môi trường dưới -30 ° С - Nhãn hiệu DA.
Nếu cần thiết, nó được phép sử dụng nhiên liệu DZ ở nhiệt độ môi trường trên + 50 ° C.
Ngoài nhiên liệu cho động cơ diesel tốc độ cao, động cơ có thể hoạt động bằng nhiên liệu phản lực TC-1 GOST 10227-62 hoặc xăng động cơ A-72 GOST 2084-67, cũng như hỗn hợp nhiên liệu được sử dụng theo bất kỳ tỷ lệ nào.
Dầu M16-IHP-3 TU 001226-75 dùng để bôi trơn động cơ. Trong trường hợp không có loại dầu này, cho phép sử dụng dầu MT-16p.
Khi thay từ loại dầu này sang loại dầu khác, phải xả hết dầu cặn từ cacte của động cơ và thùng dầu của máy.
Việc trộn lẫn các loại dầu được sử dụng với nhau, cũng như việc sử dụng các loại dầu nhãn hiệu khác đều bị cấm. Được phép trộn lẫn cặn không thoát nước của một nhãn hiệu dầu này với một nhãn hiệu dầu khác, được đổ lại trong hệ thống dầu.
Khi xả nước, nhiệt độ dầu không được thấp hơn + 40 ° C.
Để làm mát động cơ ở nhiệt độ môi trường ít nhất + 5 ° C, nước ngọt tinh khiết không có tạp chất cơ học được sử dụng, đi qua một bộ lọc đặc biệt cung cấp cho EC của máy.
Để bảo vệ động cơ khỏi bị ăn mòn và hình thành cặn bẩn, 0,15% phụ gia ba thành phần (0,05% mỗi thành phần) được thêm vào nước đi qua bộ lọc.
Phụ gia bao gồm trinatri photphat GOST 201-58, đỉnh kali crom GOST 2652-71 và natri nitrit GOST 6194-69 trước tiên phải được hòa tan trong 5-6 lít nước đi qua bộ lọc hóa học và được đun nóng đến nhiệt độ 60-80 ° C. Trong trường hợp tiếp nhiên liệu 2-3 lít, được phép (một lần) sử dụng nước không có chất phụ gia.
Không đổ phụ gia chống ăn mòn trực tiếp vào hệ thống.
Trong trường hợp không có phụ gia ba thành phần, cho phép sử dụng pic crom tinh khiết 0,5%.
Ở nhiệt độ môi trường xung quanh dưới + 50 ° C, nên sử dụng chất lỏng có độ đông thấp (chất chống đông) “40” hoặc “65” GOST 159-52. Nhãn hiệu chất chống đông "40" được sử dụng ở nhiệt độ môi trường xung quanh lên đến -35 ° C, ở nhiệt độ dưới -35 ° C - nhãn hiệu chất chống đông "65".
Đổ đầy nhiên liệu, dầu và nước làm mát vào động cơ tuân thủ các biện pháp ngăn chặn sự xâm nhập của các tạp chất cơ học và bụi cũng như độ ẩm vào nhiên liệu và dầu.
Nên tiếp nhiên liệu với sự trợ giúp của tàu chở dầu đặc biệt hoặc thiết bị tiếp nhiên liệu thông thường (khi tiếp nhiên liệu từ các thùng chứa riêng biệt).
Nhiên liệu phải được tiếp nhiên liệu qua bộ lọc lụa. Nên đổ đầy dầu với sự trợ giúp của các chất làm đầy dầu đặc biệt. Đổ đầy dầu, nước và chất lỏng ít đóng băng qua bộ lọc có lưới số 0224 GOST 6613-53.
Đổ đầy hệ thống đến mức được chỉ định trong hướng dẫn vận hành của máy.
Để lấp đầy hoàn toàn các thể tích của hệ thống bôi trơn và làm mát, sau khi tiếp nhiên liệu, hãy khởi động động cơ trong 1-2 phút, sau đó kiểm tra các mức và nếu cần, hãy tiếp nhiên liệu cho hệ thống, Trong quá trình vận hành, cần kiểm soát lượng nước làm mát và dầu trong hệ thống động cơ và duy trì mức IB của chúng trong giới hạn quy định.
Không cho phép động cơ chạy nếu có ít hơn 20 lít dầu trong thùng bôi trơn động cơ.
Nếu mức nước làm mát giảm do bay hơi hoặc rò rỉ vào hệ thống làm mát, hãy thêm nước hoặc chất chống đông tương ứng.
Xả nước làm mát và dầu qua các van xả đặc biệt của động cơ và máy (lò hơi gia nhiệt và thùng chứa dầu) bằng cách sử dụng một ống có khớp nối với các lỗ nạp mở. Để loại bỏ hoàn toàn lượng nước còn lại khỏi hệ thống làm mát nhằm tránh đóng băng, bạn nên đổ 5-6 lít chất lỏng ít đóng băng vào hệ thống.
Đặc điểm hoạt động của động cơ trên nhiều loại nhiên liệu khác nhau
Hoạt động của động cơ trên nhiều loại nhiên liệu khác nhau được thực hiện bằng cơ cấu điều khiển cấp nhiên liệu có hai vị trí để đặt cần gạt đa nhiên liệu: vận hành trên nhiên liệu cho động cơ diesel tốc độ cao, nhiên liệu cho động cơ phản lực, xăng (khi giảm công suất) và hỗn hợp của chúng theo bất kỳ tỷ lệ nào; chỉ hoạt động bằng xăng.
Nghiêm cấm thao tác trên các loại nhiên liệu khác với vị trí cần gạt này.
Việc lắp đặt cơ cấu điều khiển cấp nhiên liệu từ vị trí "Vận hành trên nhiên liệu điêzen" đến vị trí "Vận hành trên xăng" được thực hiện bằng cách vặn vít điều chỉnh của cần gạt đa nhiên liệu theo chiều kim đồng hồ cho đến khi nó dừng lại, và từ vị trí "Vận hành trên xăng "đến vị trí" Vận hành trên nhiên liệu diesel "- bằng cách xoay vít điều chỉnh cần gạt đa nhiên liệu ngược chiều kim đồng hồ cho đến khi dừng.
Tính năng khởi động và vận hành động cơ khi chạy xăng. Trước khi nổ máy ít nhất 2 phút phải bật bơm BCN của máy và bơm mạnh nhiên liệu bằng bơm mồi thủ công của máy; trong mọi trường hợp, không phụ thuộc vào nhiệt độ môi trường, trước khi khởi động, bơm dầu hai lần vào xi lanh.
Bơm ly tâm xăng của máy phải duy trì trong suốt thời gian động cơ chạy bằng xăng, hỗn hợp của nó với các nhiên liệu khác và trong thời gian dừng máy ngắn (3-5 phút).
Tốc độ không tải ổn định tối thiểu khi động cơ chạy bằng xăng là 1000 vòng / phút.
TÍNH NĂNG VẬN HÀNH
S. Suvorov nhớ lại những ưu điểm và nhược điểm của động cơ này trong cuốn sách "T-64" của mình.
Trên xe tăng T-64A, được sản xuất từ năm 1975, lớp giáp của tháp pháo cũng được tăng cường do sử dụng chất độn corundum.
Trên những cỗ máy này, dung tích thùng nhiên liệu cũng được tăng từ 1093 lít lên 1270 lít, do đó một hộp để xếp phụ tùng xuất hiện ở phía sau tháp pháo. Trên các máy của các phiên bản trước, phụ tùng và phụ kiện được đặt trong hộp trên chắn bùn bên phải, nơi lắp thêm bình xăng, kết nối với hệ thống nhiên liệu. Khi người lái xe lắp van phân phối nhiên liệu trên bất kỳ nhóm thùng nào (phía sau hoặc phía trước), nhiên liệu được sản xuất chủ yếu từ các thùng bên ngoài.
Một cặp bánh răng sâu đã được sử dụng trong cơ cấu căng đường ray, cho phép nó hoạt động mà không cần bảo dưỡng trong suốt thời gian sử dụng của xe tăng.
Các đặc tính hiệu suất của các máy này đã được cải thiện rất nhiều. Vì vậy, ví dụ, thử nghiệm trước dịch vụ số tiếp theo đã được tăng từ 1500 và 3000 km lên 2500 và 5000 km cho T01 và TO, tương ứng. Để so sánh, trên xe tăng T-62 TO1 TO2 được thực hiện sau 1000 và 2000 km chạy, và trên xe tăng T-72 - sau 1600-1800 và 3300-3500 km, tương ứng. Thời hạn bảo hành cho động cơ 5TDF được tăng từ 250 lên 500 giờ, thời hạn bảo hành cho toàn bộ máy là 5.000 km.
Nhưng trường học chỉ là khúc dạo đầu, hoạt động chính bắt đầu trong quân đội, nơi tôi kết thúc sau khi tốt nghiệp đại học năm 1978. Ngay trước khi tốt nghiệp, chúng tôi đã được thông báo về lệnh của Tổng tư lệnh Lực lượng Mặt đất rằng những sinh viên tốt nghiệp của trường chúng tôi chỉ được phân bổ đến những đội hình có xe tăng T-64. Điều này là do trong quân đội đã có những trường hợp xe tăng T-64 bị hỏng hàng loạt, cụ thể là động cơ 5TDF. Lý do - sự thiếu hiểu biết về vật liệu và quy tắc hoạt động của những chiếc xe tăng này. Việc áp dụng xe tăng T-64 có thể so sánh với sự chuyển đổi trong ngành hàng không từ động cơ piston sang động cơ phản lực - các cựu chiến binh hàng không nhớ nó như thế nào.
Đối với động cơ 5TDF, có hai lý do chính dẫn đến sự thất bại của nó trong quân đội - quá nóng và mài mòn do bụi. Cả hai nguyên nhân đều do thiếu hiểu biết hoặc không tuân thủ các quy tắc điều hành. Hạn chế chính của engine này là nó không được thiết kế quá dành cho những kẻ ngu ngốc, đôi khi nó yêu cầu họ phải thực hiện những gì được ghi trong hướng dẫn vận hành. Khi tôi đã là chỉ huy của một đại đội xe tăng, một trong những chỉ huy trung đội của tôi, tốt nghiệp Trường xe tăng Chelyabinsk, nơi đào tạo sĩ quan cho xe tăng T-72, bằng cách nào đó bắt đầu chỉ trích nhà máy điện của xe tăng T-64. Anh không thích động cơ và tần suất bảo dưỡng của nó. Nhưng khi anh ta được hỏi câu hỏi "Đã bao nhiêu lần trong sáu tháng, bạn mở mui của chiếc MTO trên ba chiếc xe tăng huấn luyện của mình và nhìn vào khoang truyền động cơ?" Hóa ra là không bao giờ. Và những chiếc xe tăng đã tham gia huấn luyện chiến đấu.
Và cứ thế theo thứ tự. Quá nhiệt của động cơ xảy ra vì một số lý do. Đầu tiên, người thợ đã quên tháo tấm lót ra khỏi bộ tản nhiệt và sau đó không nhìn vào các thiết bị, nhưng điều này rất hiếm khi xảy ra và như một quy luật, vào mùa đông. Điều thứ hai và chính là làm đầy với chất làm mát. Theo hướng dẫn, nó phải đổ đầy nước (trong thời gian hoạt động vào mùa hè) với một chất phụ gia ba thành phần, và nước phải được đổ đầy qua một bộ lọc sulfat đặc biệt, mà tất cả các máy phát hành sớm đều được trang bị và trên máy mới. mỗi công ty phát hành một bộ lọc như vậy (10-13 bể). Các động cơ bị hỏng, chủ yếu là do các xe tăng của nhóm tác chiến huấn luyện, hoạt động ít nhất năm ngày một tuần và thường được đặt tại các phạm vi trong công viên dã chiến. Đồng thời, "sách giáo khoa" lái xe-cơ khí (gọi là cơ khí của máy đào tạo), như một quy luật, những người lao động chăm chỉ và có lương tâm, nhưng không biết sự phức tạp của động cơ, đôi khi có thể đổ nước vào. hệ thống làm mát chỉ từ vòi, đặc biệt là vì bộ lọc sulfat (mỗi công ty một cái) thường được cất giữ trong các khu mùa đông, ở đâu đó trong tủ của giám đốc kỹ thuật của công ty. Kết quả là hình thành cặn trong các rãnh mỏng của hệ thống làm mát (ở khu vực buồng đốt), thiếu sự lưu thông chất lỏng ở phần nóng nhất của động cơ, quá nhiệt và hỏng hóc động cơ. Sự hình thành cáu cặn ngày càng trầm trọng hơn do nước ở Đức rất cứng.
Một khi ở một đơn vị lân cận, động cơ đã bị loại bỏ do quá nóng do lỗi của trình điều khiển. Khi phát hiện ra một rò rỉ nhỏ của chất làm mát từ bộ tản nhiệt, theo lời khuyên của một trong những "chuyên gia" để thêm mù tạt vào hệ thống, anh ta đã mua một gói mù tạt trong cửa hàng và đổ tất cả vào hệ thống, kết quả là - bị tắc. của các kênh và lỗi động cơ.
Cũng có những bất ngờ khác với hệ thống làm mát. Đột nhiên, nó bắt đầu đẩy chất làm mát ra khỏi hệ thống làm mát thông qua van hơi-không khí (PVK). Một số, không hiểu vấn đề là gì, cố gắng bắt đầu nó từ sự giằng co - kết quả của sự phá hủy động cơ. Vì vậy, tiểu đoàn phó của tôi đã làm cho tôi một món quà "Tết", và tôi phải thay đổi động cơ vào ngày 31 tháng Chạp. Tôi đã có thời gian trước năm mới, bởi vì Thay thế động cơ trên xe tăng T-64 không phải là một thủ tục quá phức tạp và quan trọng nhất là không cần phải căn chỉnh khi lắp đặt. Hầu hết thời gian khi thay động cơ trên xe tăng T-64, cũng như trên tất cả các xe tăng trong nước, đều được thực hiện bằng quy trình xả và tiếp nhiên liệu cũng như chất làm mát. Nếu xe tăng của chúng ta có đầu nối với van thay vì đầu nối kép, như trên Leopards hoặc Leclerc, thì việc thay thế động cơ trên xe tăng T-64 hoặc T-80 kịp thời sẽ không mất nhiều thời gian hơn là thay thế toàn bộ bộ nguồn trên xe tăng phương Tây. Ví dụ, vào ngày đáng nhớ đó, ngày 31 tháng 12 năm 1980, sau khi xả sạch dầu và nước làm mát, Cảnh sát viên E. Sokolov và tôi đã "ném" động cơ ra khỏi MTO chỉ trong 15 phút.
Nguyên nhân thứ hai dẫn đến hỏng hóc động cơ 5TDF là do bụi bẩn. Hệ thống lọc không khí. Nếu bạn không kiểm tra mức nước làm mát kịp thời mà nên kiểm tra trước mỗi lần thoát ra của máy, thì có thể sẽ đến lúc không còn chất lỏng ở phần trên của áo làm mát và xảy ra hiện tượng quá nhiệt cục bộ. Trong trường hợp này, điểm yếu nhất là vòi phun. Trong trường hợp này, các gioăng kim phun bị cháy hoặc bản thân kim phun bị hỏng, sau đó thông qua các vết nứt trên đó hoặc gioăng bị cháy, khí từ các xi lanh đi vào hệ thống làm mát và dưới áp suất của chúng, chất lỏng được đẩy ra ngoài qua PVCL. Tất cả điều này không gây tử vong cho động cơ và được loại bỏ nếu có một người hiểu biết trong đơn vị. Trên động cơ thẳng hàng và hình chữ V thông thường trong tình huống tương tự, "dẫn" miếng đệm đầu xi-lanh, và trong trường hợp này sẽ phải làm việc nhiều hơn.
Nếu trong trường hợp như vậy động cơ bị dừng và không có biện pháp xử lý thì sau một thời gian các xi lanh sẽ bắt đầu nạp đầy chất làm mát, động cơ là một bộ ghi quán tính và một bộ lọc không khí lốc xoáy. Máy lọc không khí, theo hướng dẫn vận hành, được xả khi cần thiết. Trên xe tăng loại T-62, nó được rửa sạch vào mùa đông sau 1000 km và vào mùa hè sau 500 km. Trên xe tăng T-64 - khi cần thiết. Đây là nơi mà sự vấp ngã xuất hiện - một số coi đó là thực tế rằng bạn không cần phải rửa nó. Nhu cầu phát sinh khi dầu đi vào lốc xoáy. Và nếu ít nhất một trong số 144 lốc chứa dầu, thì máy lọc không khí phải được xả, bởi vì qua lốc xoáy này, không khí không sạch có bụi đi vào động cơ, và sau đó, giống như đá nhám, lót xi lanh và vòng piston bị xóa. Động cơ bắt đầu mất công suất, tiêu thụ dầu tăng lên, và sau đó ngừng khởi động hoàn toàn.
Không khó để kiểm tra sự xâm nhập của dầu vào lốc máy - chỉ cần nhìn vào cửa hút gió của lốc máy trên bộ lọc không khí. Thông thường, họ nhìn vào ống xả bụi từ máy lọc không khí, và nếu thấy dầu dính trên đó, thì họ nhìn vào máy lọc không khí, và nếu cần, hãy rửa nó. Dầu đến từ đâu? Thật đơn giản: cổ nạp của bình dầu của hệ thống bôi trơn động cơ nằm bên cạnh lưới hút gió. Khi tiếp nhiên liệu bằng dầu, một bình tưới cây thường được sử dụng, nhưng vì Một lần nữa, trên các máy tập, bình tưới cây, theo quy luật, không có (ai đó làm mất, có người đặt nó vào dây đai bánh xích, quên và lái xe qua nó, v.v.), khi đó thợ máy chỉ cần đổ dầu từ xô, trong khi dầu tràn., đầu tiên rơi vào lưới hút gió, và sau đó rơi vào bộ lọc không khí. Ngay cả khi đổ đầy dầu qua bình tưới nhưng trong thời tiết có gió, gió làm văng dầu lên lưới lọc không khí. Vì vậy, khi đổ dầu, tôi đã yêu cầu cấp dưới đặt một tấm lót của các phụ tùng và phụ kiện của bình lên lưới hút gió, nhờ đó tôi tránh được rắc rối do bụi bám vào động cơ. Cần lưu ý rằng điều kiện bụi ở Đức vào mùa hè là khắc nghiệt nhất. Vì vậy, ví dụ, trong cuộc tập trận của sư đoàn vào tháng 8 năm 1982, khi thực hiện một cuộc hành quân qua các khu rừng của Đức, vì bụi bay mù mịt, người ta thậm chí không nhìn thấy nòng súng của xe tăng mình kết thúc ở đâu. Khoảng cách giữa những chiếc xe trong cột được giữ lại theo đúng nghĩa đen của mùi hương. Khi chỉ còn vài mét nữa là đến thùng dẫn đầu, có thể phát hiện ra mùi khí thải và phanh kịp thời. Và như vậy là 150 km. Sau cuộc tuần hành, tất cả mọi thứ: xe tăng, người và khuôn mặt của họ, quần yếm và ủng đều có màu giống nhau - màu của bụi đường.
Diesel 6TD
Đồng thời với việc thiết kế và cải tiến công nghệ của động cơ diesel 5TDF, nhóm thiết kế KKBD đã bắt đầu phát triển mô hình tiếp theo của động cơ diesel 2 thì có thiết kế 6 xi-lanh với công suất tăng lên đến 735 kW (1000 mã lực). Động cơ này, giống như 5TDF, là động cơ diesel với các xi lanh được bố trí theo chiều ngang, các piston chuyển động ngược chiều và thổi dòng trực tiếp. Động cơ diesel được đặt tên là 6TD.
Quá trình tăng áp được thực hiện từ một máy nén cơ học (lò xo) nối với tuabin khí, biến đổi một phần nhiệt năng của khí thải thành công cơ học để dẫn động máy nén.
Vì công suất do tuabin phát triển không đủ để dẫn động máy nén, nên nó được kết nối với cả hai trục khuỷu của động cơ bằng hộp số và cơ cấu truyền động. Tỷ lệ nén được lấy là 15.
Để có được thời gian van cần thiết, tại đó việc làm sạch xi lanh cần thiết khỏi khí thải và nạp đầy khí nén sẽ được cung cấp, dịch chuyển góc của trục khuỷu được cung cấp (như trên động cơ 5TDF) kết hợp với sự bố trí không đối xứng của cửa nạp. và các cổng xả của xi lanh dọc theo chiều dài của chúng. Mômen xoắn lấy từ trục khuỷu là 30% đối với trục nạp và 70% đối với mômen xả của động cơ. Mômen xoắn phát triển trên trục nạp được truyền qua bộ truyền bánh răng đến trục xả. Tổng mô-men xoắn có thể được lấy từ cả hai đầu của trục xả thông qua ly hợp ngắt điện.
Vào tháng 10 năm 1979, động cơ 6TD, sau khi sửa đổi nghiêm túc nhóm xi-lanh-pít-tông, thiết bị nhiên liệu, hệ thống cung cấp không khí và các bộ phận khác, đã vượt qua thành công các bài kiểm tra giữa các khoang. Kể từ năm 1986, động cơ sê-ri 55 đầu tiên đã được sản xuất. Trong những năm tiếp theo, sản lượng hàng loạt tăng lên và đạt đỉnh vào năm 1989.
Tỷ lệ hợp nhất từng phần của 6TD với động cơ diesel 5TDF là hơn 76% và độ tin cậy khi vận hành không thấp hơn so với động cơ 5TDF đã được sản xuất hàng loạt trong nhiều năm.
Công việc của KHKBD dưới sự lãnh đạo của nhà thiết kế chính N. K. Ryazantsev nhằm cải tiến hơn nữa động cơ diesel cho xe tăng 2 kỳ vẫn tiếp tục. Các đơn vị, cơ chế và hệ thống đang được hoàn thiện, theo đó các lỗi riêng lẻ đã được xác định trong quá trình vận hành. Hệ thống điều áp đã được cải thiện. Nhiều cuộc thử nghiệm động cơ đã được thực hiện với sự thay đổi thiết kế.
Một sửa đổi mới của động cơ diesel, 6TD-2, đang được phát triển. Công suất của nó không còn là 735 kW (1000 mã lực) như ở 6TD, mà là 882 kW (1200 mã lực). Sự thống nhất chi tiết của nó với động cơ diesel 6TD được cung cấp hơn 90% và với động cơ diesel 5TDF - hơn 69%.
Không giống như động cơ 6TD, động cơ 6TD-2 sử dụng máy nén ly tâm hướng trục 2 cấp của hệ thống điều áp và những thay đổi trong thiết kế của tuabin, ống thổi, bộ lọc dầu ly tâm, ống nhánh và các đơn vị khác. Tỷ lệ nén cũng giảm nhẹ - từ 15 xuống 14,5 và áp suất hiệu dụng trung bình được tăng từ 0,98 MPa lên 1,27 MPa. Mức tiêu thụ nhiên liệu cụ thể của động cơ 6TD-2 là 220 g / (kW * h) (162 g / (hp * h)) thay vì 215 g / (kW * h) (158 g / (hp * h)) - cho 6TD. Từ quan điểm lắp đặt trong xe tăng, động cơ diesel 6TD-2 hoàn toàn có thể hoán đổi cho động cơ 6DT.
Năm 1985, Diesel 6TD-2 đã vượt qua các bài kiểm tra giữa các phòng và tài liệu thiết kế đã được đệ trình để chuẩn bị và tổ chức sản xuất hàng loạt.
Tại KKBD, với sự tham gia của NIID và các tổ chức khác, công việc nghiên cứu và phát triển trên động cơ diesel 2 thì 6TD được tiếp tục với mục đích nâng công suất của nó lên 1103 kW (1500hp), 1176 kW (1600hp), 1323 kW (1800hp) với việc thử nghiệm trên các mẫu, cũng như tạo ra trên cơ sở dòng động cơ cho VGM và các máy kinh tế quốc dân. Đối với VGM hạng nhẹ và hạng trung bình, động cơ diesel 3TD có công suất 184 … 235 kW (250-320hp), 4TD với công suất 294 … 331 kW (400 … 450hp) đã được phát triển. Một biến thể của động cơ diesel 5DN với công suất 331… 367 kW (450-500 mã lực) cho xe bánh lốp cũng được phát triển. Đối với những người vận chuyển máy kéo và xe kỹ thuật, một dự án đã được phát triển cho động cơ diesel 6DN với công suất 441 … 515 kW (600-700 mã lực).
Diesel 3TD
Động cơ ZTD thiết kế ba xi lanh là thành viên của một loạt thống nhất duy nhất với các động cơ nối tiếp 5TDF, 6TD-1 và 6TD-2E. Vào đầu những năm 60, một nhóm động cơ dựa trên 5TDF đã được tạo ra ở Kharkov cho các loại xe hạng nhẹ (xe bọc thép chở quân, xe chiến đấu bộ binh, v.v.) và hạng nặng (xe tăng, 5TDF, 6TD).
Những động cơ này có một sơ đồ thiết kế duy nhất:
- chu kỳ hai kỳ;
- sự sắp xếp theo chiều ngang của các xi lanh;
- độ chặt cao;
- truyền nhiệt thấp;
- khả năng sử dụng ở nhiệt độ môi trường xung quanh
môi trường từ âm 50 đến cộng 55 ° С;
- giảm công suất thấp ở nhiệt độ cao
môi trường;
- đa nhiên liệu.
Ngoài những nguyên nhân khách quan, những sai lầm còn mắc phải trong quá trình chế tạo dòng động cơ diesel boxer hai kỳ 3TD vào giữa những năm 60. Ý tưởng về động cơ 3 xi-lanh đã được thử nghiệm trên cơ sở 5 xi-lanh, trong đó hai xi-lanh bị bóp nghẹt. Đồng thời, đường dẫn khí và bộ phận điều áp không được phối hợp với nhau. Đương nhiên, sức mạnh của tổn thất cơ học cũng được tăng lên.
Trở ngại chính đối với việc tạo ra một dòng động cơ thống nhất trong những năm 60 và 70 là thiếu một chương trình rõ ràng cho việc phát triển chế tạo động cơ trong nước; giới lãnh đạo đã “xáo trộn” giữa các khái niệm khác nhau về động cơ diesel và động cơ tuabin khí.. Vào những năm 70, khi Leonid Brezhnev lên lãnh đạo đất nước, tình hình càng trở nên trầm trọng hơn, việc sản xuất song song các loại xe tăng với các động cơ khác nhau - T-72 và T-80, theo đặc điểm của chúng là "xe tăng tương tự" của đã được sản xuất T- 64. Không còn bàn cãi gì về việc thống nhất động cơ của xe tăng, xe chiến đấu bộ binh và xe bọc thép chở quân.
Thật không may, tình trạng tương tự cũng xảy ra ở các chi nhánh khác của tổ hợp công nghiệp-quân sự - đồng thời, các phòng thiết kế khác nhau đang được phát triển trong lĩnh vực chế tạo tên lửa, máy bay, trong khi những người tốt nhất không được chọn trong số đó mà là các sản phẩm tương tự từ các Cục Thiết kế khác nhau (Phòng thiết kế) được sản xuất song song.
Chính sách như vậy là khởi đầu cho sự kết thúc của nền kinh tế trong nước, và là lý do dẫn đến sự tụt hậu trong việc chế tạo xe tăng, thay vì đoàn kết thành một "nắm đấm duy nhất", các nỗ lực đã bị phân tán vào sự phát triển song song của các phòng thiết kế cạnh tranh.
Xe hạng nhẹ (LME), được sản xuất từ những năm 60 … 80 của thế kỷ trước, có động cơ kiểu dáng lạc hậu, cung cấp mật độ công suất trong khoảng 16-20 mã lực / tấn. Máy móc hiện đại nên có công suất cụ thể từ 25-28 mã lực / tấn, điều này sẽ làm tăng khả năng cơ động của chúng.
Trong những năm 90, 2000, việc hiện đại hóa LME trở nên phù hợp - BTR-70, BTR-50, BMP-2.
Trong giai đoạn này, các cuộc thử nghiệm đối với những cỗ máy này đã được thực hiện, cho thấy những đặc tính cao của động cơ mới, nhưng đồng thời, một số lượng lớn động cơ UTD-20S1 đã được cất giữ và sản xuất trên lãnh thổ Ukraine sau khi bị sập. của Liên Xô.
Tổng thiết kế chế tạo xe tăng của Ukraine M. D. Borisyuk (KMDB) quyết định sử dụng các động cơ nối tiếp hiện có - SMD-21 UTD-20 và "Deutz" của Đức để hiện đại hóa các máy này.
Mỗi phương tiện đều có động cơ riêng không thống nhất với nhau và với động cơ đã có trong quân đội. Nguyên nhân là do các nhà máy sửa chữa của Bộ Quốc phòng sử dụng động cơ có sẵn tại kho của khách hàng sẽ có lãi, giảm chi phí công việc.
Nhưng vị trí này đã tước quyền công tác của Doanh nghiệp Nhà nước “Nhà máy mang tên V. A. Malysheva”và trên hết là nhà máy tổng hợp.
Vị trí này hóa ra là không rõ ràng - một mặt là tiết kiệm, mặt khác, làm mất đi quan điểm.
Điều đáng chú ý là trong KMDB liên quan đến 3TD, một số yêu cầu đã được đưa ra (đối với tiếng ồn và khói), đã được chấp nhận và loại bỏ.
Để giảm khói trong quá trình khởi động và ở chế độ nhất thời, thiết bị nhiên liệu kín đã được lắp đặt trên động cơ ZTD và mức tiêu thụ dầu đã giảm đáng kể. Giảm tiếng ồn được đảm bảo bằng cách giảm áp suất đốt cháy tối đa và giảm khe hở trong cặp piston-xi lanh trên động cơ 280 và 400 mã lực, cũng như giảm phạm vi dao động xoắn
Việc giảm tiêu thụ dầu trên động cơ ZTD đạt được do các yếu tố sau:
- giảm số lượng xi lanh;
- việc sử dụng một piston có thân bằng gang thay vì hợp kim nhôm;
- tăng áp suất riêng của vòng gạt dầu bằng cách
thành xi lanh.
Kết quả của các biện pháp được thực hiện, mức tiêu thụ dầu tương đối trên động cơ ZTD tiếp cận với mức tiêu thụ trên động cơ cho các mục đích kinh tế quốc dân.